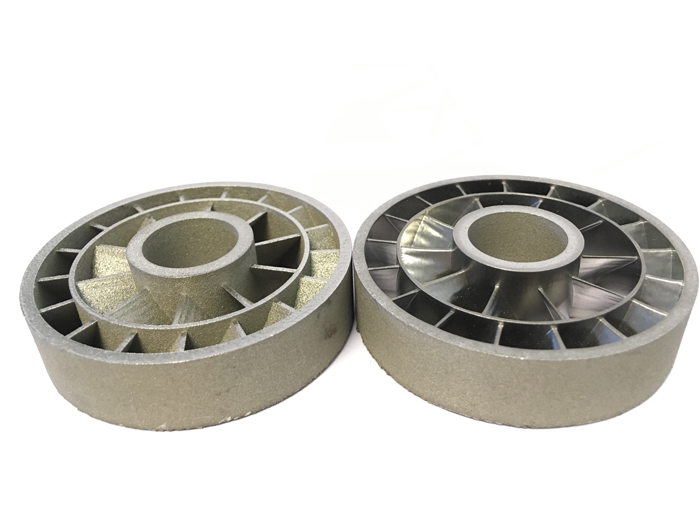
Finishing technologies for additive layer components.
Extrude Hone AFM finishing solution for additive layer components.
3D Printing has revolutionized the engineering and manufacturing arena for many industries, particularly aerospace, medical and automotive. Additive Manufacturing offers unprecedented freedom of design, rapid prototyping capabilities and a huge scope for light-weighting of components.
Additive Manufacturing is no longer just a prototyping tool and is being used in serial production for real-life applications.
Despite the obvious benefits of 3D Printing, like with most emergent technologies, there are also significant challenges to overcome.
Additive Manufacturing technologies produce parts with reasonably rough surfaces, and expensive and time-consuming post-processing technologies are often required to reach the strict surface finish tolerances of many applications to make the components fit for use. Depending on the application, excellent surface finish is typically required to improve flow (either air or fluid), increase fatigue strength or ensure cleanliness.
Extrude Hone has two solutions to address the challenge of 3D Printing component finishing, namely Abrasive Flow Machining (AFM) and COOLPULSE.
AFM uses a non-Newtonian, visco-elastic fluid loaded with abrasive particles which, when put under pressure, acts like a solid. When this non-Newtonian material is forced over a surface, it stiffens, holds the abrasive particles in situ, and abrades the surface as it flows.
In the example pictured above, we were able to reduce the surface roughness of this Selective Laser Melted (SLM) aluminium impeller produced by TWI in Catcliffe, UK from average 11.95 Ra to 0.95 Ra with only a 15-minute processing time.
This job has been performed in our Milton Keynes, UK Contract Shop.
With AFM you achieve a surface finish that is more consistent, more repeatable and with much shorter cycle times than manual polishing or mass-finishing methods.
Benefits of AFM for Additive manufacturing parts:
- 10x improvement of Ra value possible
- Finish hard-to-reach internal surfaces
- Consistent and repeatable
- Short cycle times
- Feasibility and subcontract services available
By using one of Extrude Hone’s subcontract shops, companies can take advantage of our many years of application engineering experience to get the right solution for their 3D Printing finishing needs.
Being a global player, Extrude Hone is uniquely positioned to offer capital equipment, after-market support and subcontracting services to customers all over the world.
For information on our ECM technology for 3D Printed components COOLPULSE