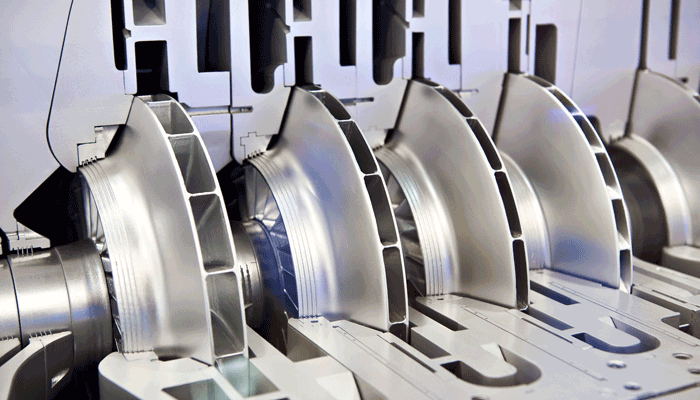
BESCAST Precision Investment Casting : pourquoi la contribution d’Extrude Hone en vaut la peine.
Aujourd’hui, nous nous intéressons à l’un de nos fantastiques clients, BESCAST, une entreprise basée à Willoughby, dans l’Ohio, aux États-Unis.
Son PDG, Dave Palivec, répondra à nos questions, notamment sur les roues de compresseurs et sur les avantages de l’usinage par extrusion de pâte abrasive dans l’industrie pétrolière.
Qui est Bescast?
Bescast a été fondée en 1945 et s’est développée pour devenir une entreprise de moulage de précision à la pointe de la technologie, d’une superficie de 7500 mètres carrés, l’une des plus avancées au monde.
Bescast se spécialise dans les configurations de profils aérodynamiques moulés, en mettant l’accent sur les composants de moteurs et de compresseurs de turbines à gaz. Les exemples comprennent :
- roues de compresseurs intégralement moulées,
- roues de turbine,
- tuyères de turbine,
- roues de pompes à carburant,
- roues de compresseurs de gaz carénées,
- et les tourbillons de combustion.

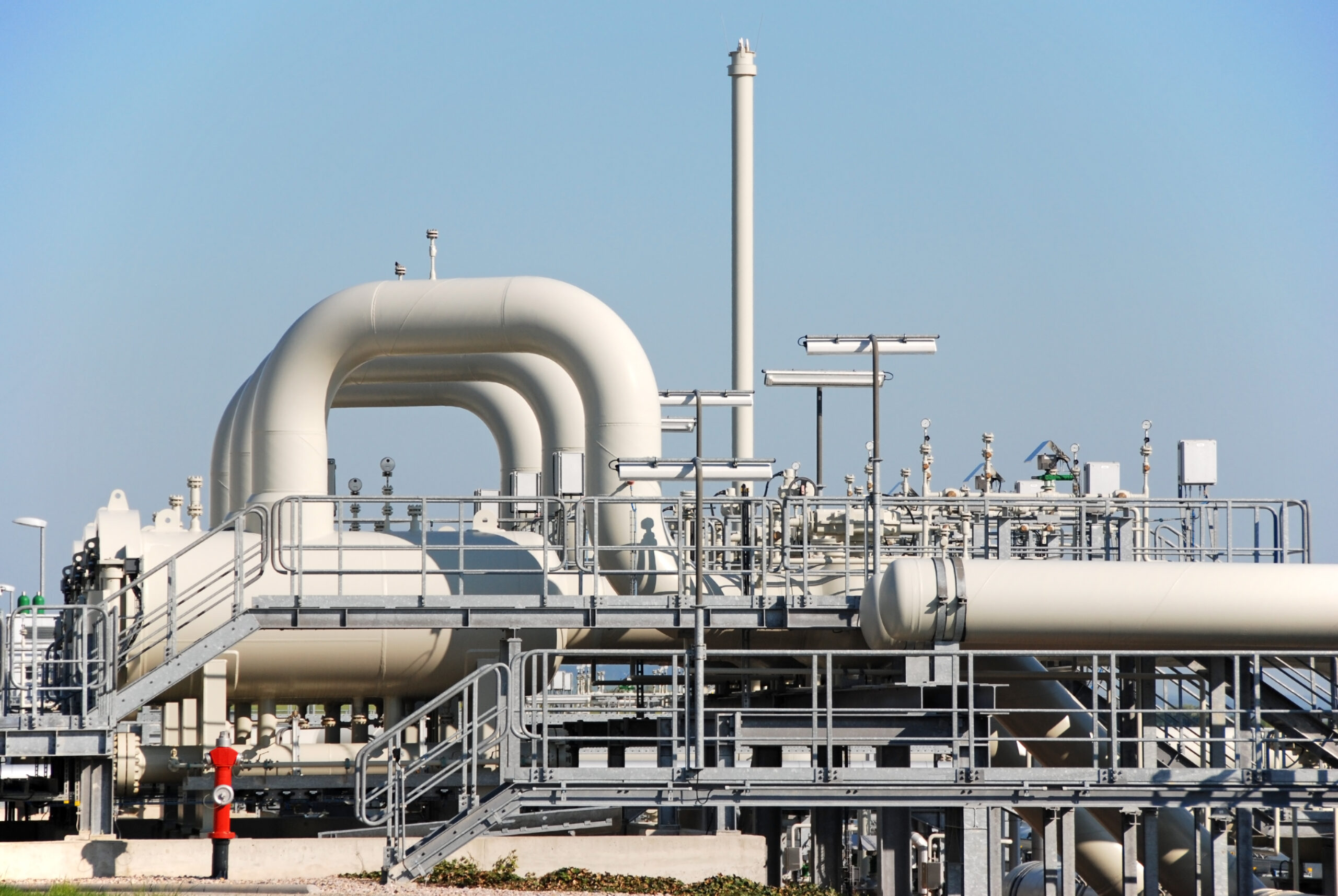
Comme nous l’avons dit, nous nous concentrerons sur les roues centrifuges de compresseurs pour les entreprises du secteur de l’énergie des turbines à gaz dans la suite de l’article et de l’interview. Ces roues sont couramment utilisées dans les compresseurs associés à une turbine à gaz terrestre.
Attendez une seconde, avant que nous plongions dans l’interview de Dave Palivec. Avant cela, nous pouvons peut-être dire quelques mots sur le moulage de précision à modèle perdu, une technique haut de gamme.
Qu’est-ce que le moulage de précision à la cire perdue ?
Avez-vous besoin de pièces au design complexe et aux parois minces?
Votre application exige-t-elle un moulage précis avec des tolérances extrêmement serrées?
Il peut être difficile de fabriquer de tels composants, mais le processus de moulage à la cire perdue peut être la solution pour de nombreuses applications difficiles.
Le moulage à la cire perdue permet de produire des pièces présentant des tolérances serrées, un excellent état de surface et des géométries complexes.
Ce processus implique de :
- Produire une matrice de moulage à la cire perdue sur la base d’un maître modèle correspondant au produit final, en tenant compte du rétrécissement.
- Créer un modèle en cire de la pièce pour reproduire le produit.
- Assembler les modèles en cire, les attacher à la carotte pour créer une arborescence qui permettra au métal en fusion de s’écouler dans chaque partie de la pièce moulée.
- Enduire la cire d’un matériau céramique réfractaire pour former la coquille.
- Faire fondre la coquille de cire pour obtenir un moule creux correspondant à la forme des composants souhaités.
- Couler le métal en fusion dans le moule après avoir chauffé la coquille.
- Refroidir la coquille pour la solidifier.
- Enlever la couche de céramique.
- Finir de la pièce. L’amélioration de la surface comprend la correction des défauts de surface, l’amélioration de la rugosité de la surface, l’application d’un traitement thermique et un usinage mineur.
Entretien avec Dave Palivec, PDG de Bescast.
Bruno Boutantin Extrude Hone: Dave, présentez-vous brièvement.
Dave Palivec : Je suis le président-directeur général de Bescast, Inc. Je travaille pour la société depuis septembre 2021 et, avant cela, j’étais impliqué dans la fabrication depuis 1989. J’ai passé la plus grande partie de mon temps dans des fonderies, en commençant par le moulage sous pression et plus récemment (de 2015 à aujourd’hui) dans le moulage à la cire perdue.
BB : Aujourd’hui, nous avons décidé de nous concentrer sur les roues des compresseurs. Ces composants essentiels sont combinés en plusieurs étapes, jusqu’à 10, dans les compresseurs qui doivent offrir un rendement élevé. Quel est le défi que représente la production de ces roues ?
DP : L’un des principaux défis liés à la production de ce type de pièces critiques est la présence de corps étrangers (fragments de céramique en suspension dans le métal en fusion pendant le processus de coulée).
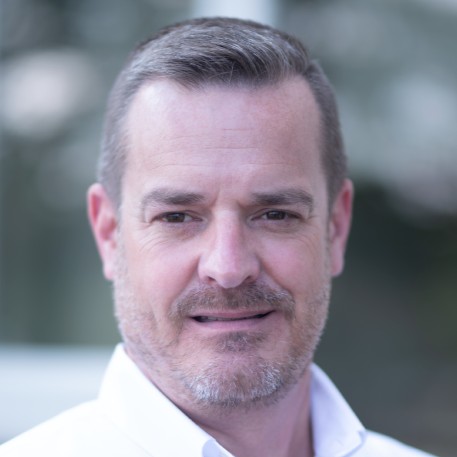
Ces fragments ne sont pas autorisés par les exigences du client, ils doivent donc être meulés et soudés en réparation. Souvent, ces fragments se trouvent juste en dessous de la surface “telle que coulée” et ne sont pas facilement détectables sans soumettre les pièces à des essais non destructifs (END).
Les défauts latents (sous la surface) peuvent être difficiles à voir et nécessitent souvent un enlèvement de matière excessif à l’aide d’une meuleuse.
L’utilisation du procédé d’usinage par flux abrasif Extrude-Hone (AFM) nous permet d’accélérer la découverte de ces petits défauts, de sorte que nous pouvons commencer le processus de réparation par soudures plus tôt, ce qui permet d’améliorer la vitesse d’acheminement des pièces dans l’usine.
BB : Pourquoi l’amélioration de la surface de la roue est-elle essentielle ?
DP : L’uniformité de la pièce est essentielle pour l’application, de sorte que le processus doit être très contrôlé et reproductible. Ces produits doivent répondre à des exigences critiques en matière de débit et de pression, de sorte que des volumes de passage constants sont indispensables.
BB: Pourquoi l’amélioration manuelle des surfaces n’est-elle pas la solution idéale ?
DP : Le meulage manuel des défauts peut prendre beaucoup de temps et permettre un degré élevé de variation en fonction de l’expérience de l’opérateur. L’usinage par flux abrasif permet un processus très contrôlé et reproductible, de sorte que nous pouvons minimiser les temps de contact avec le produit.
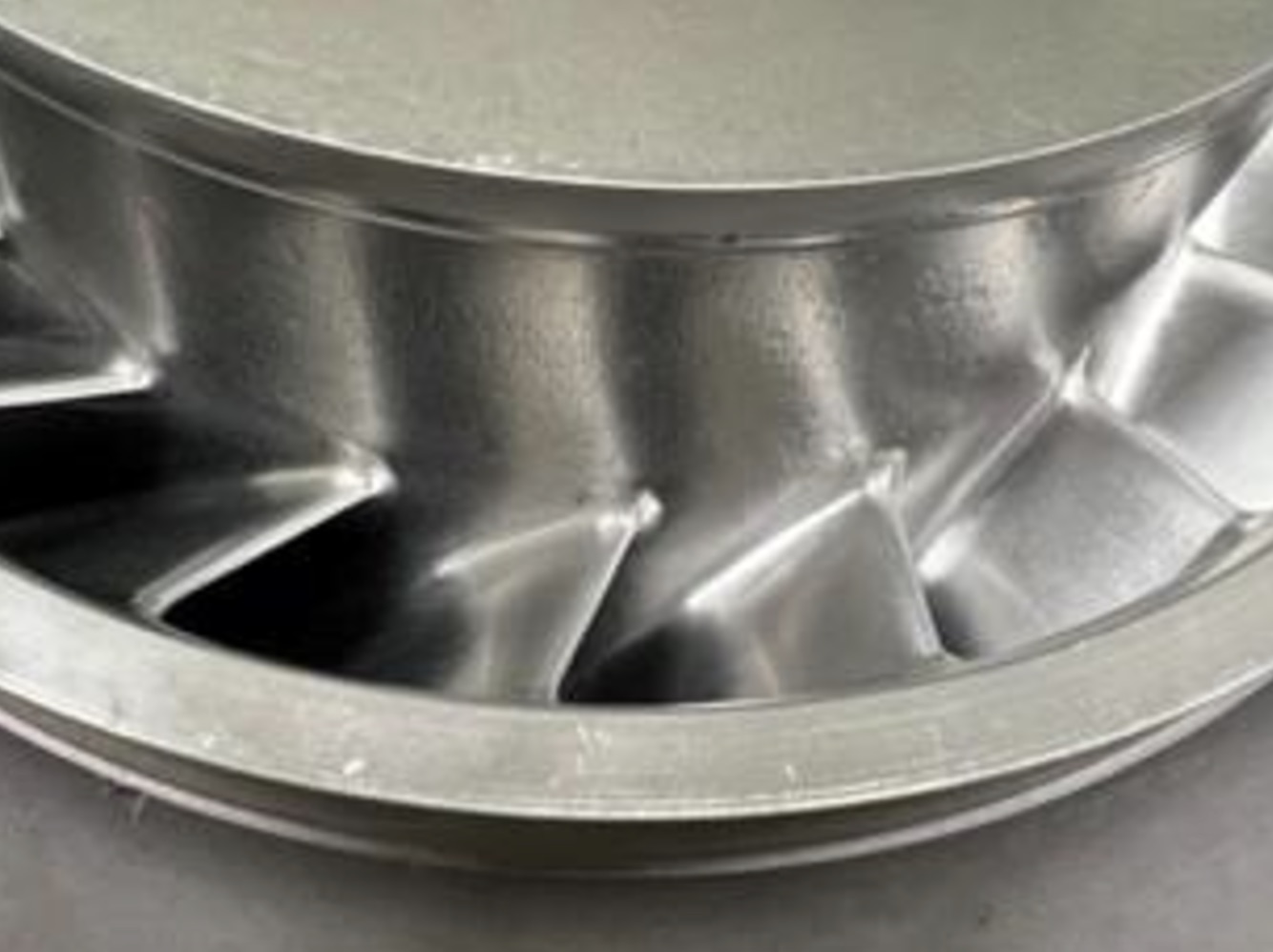
BB : Quelles sont les alternatives de finition manuelle que vous avez étudiées avant de choisir l’usinage par flux abrasif ?
DP : Nous avons expérimenté l’équipement vibratoire abrasif, divers types de bavures de meulage et d’équipement, qui ne peuvent pas remplacer la qualité et la répétabilité que nous obtenons avec Extrude-Hone.
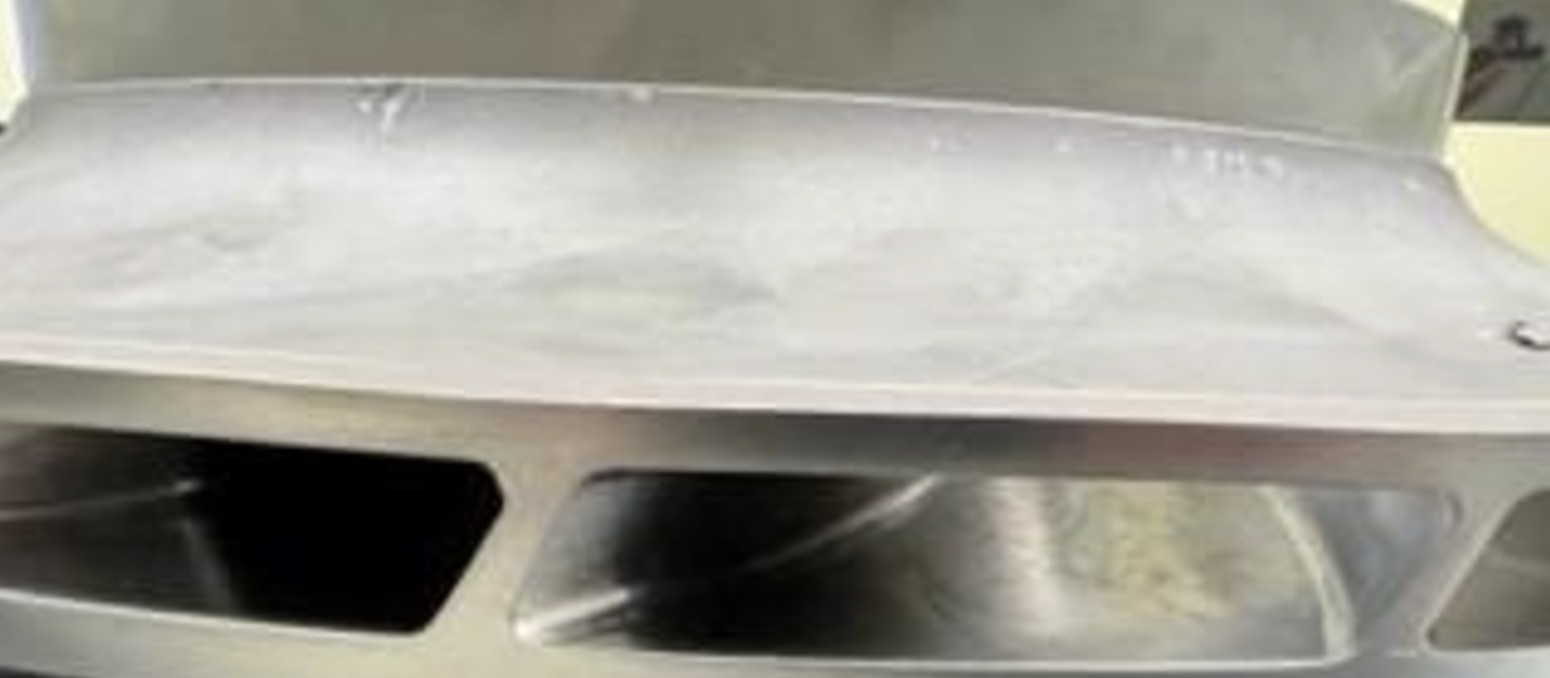
BB : Comment avez-vous connu Extrude Hone ? Comment s’est déroulée la prise de contact avec nous ?
DP : Je suis un passionné de sport automobile et je connaissais ce procédé car il est utilisé dans les passages de culasse, les pompes à jet à flux axial pour les jetskis et diverses autres applications.
BB : Quelle est votre expérience globale avec Extrude Hone ?
DP : Extrude-Hone s’est avéré être un très bon partenaire pour Bescast. Ils se sont montrés très prompts lors de la phase de démarrage et ont maintenu ce sentiment d’urgence tout au long de notre relation.
Ils sont très réactifs et ont passé beaucoup de temps à travailler avec les membres de notre équipe d’ingénieurs afin d’optimiser l’utilisation de l’AFM pour les produits de nos clients.
BB : Quels autres composants de moulage à la cire perdue seraient de bons candidats pour l’AFM, étant donné que vous produisez des pièces différentes ?
DP : Nous continuons à rechercher des applications qui nous permettraient de tirer parti du processus AFM. Nous fabriquons de nombreuses familles différentes de pièces pour les systèmes de carburant des moteurs à turbine, et nous sommes donc optimistes quant à notre capacité à exploiter cette technologie à l’avenir.
BB : Quel est l’avenir de Bescast aujourd’hui ? Avez-vous d’autres idées à partager ?
DP : Bescast a connu une croissance record au cours des deux dernières années et nous prévoyons une année 2025 nettement meilleure. Nous sommes donc très heureux d’avoir un partenaire comme Extrude-Hone qui est prêt à faire tout ce qui est nécessaire pour nous soutenir dans l’avenir.
BB : Merci, Dave, d’avoir pris le temps de nous donner un aperçu du moulage de précision à la cire perdue des roues de compresseurs.
Apprenez en plus sur la finition des roues centrifuges par Extrude Hone, ou contactez-nous.
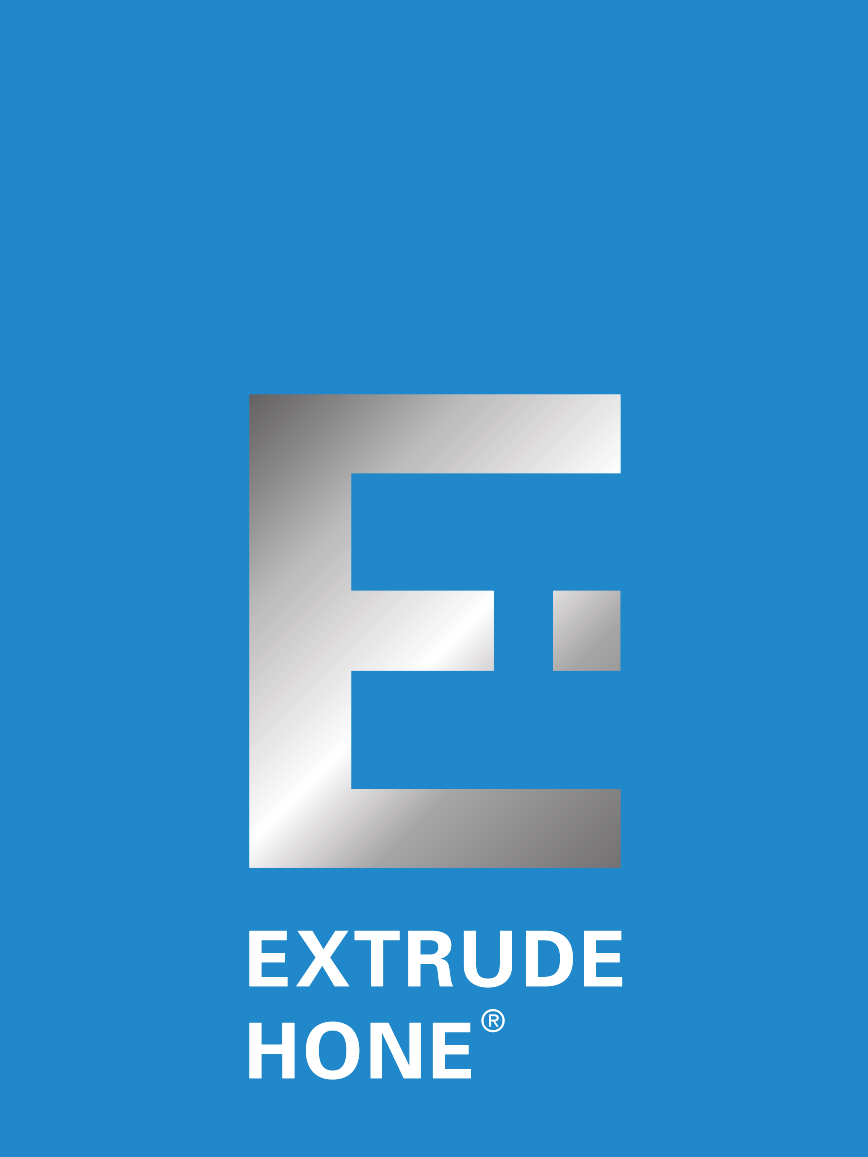
Interviewer :
Bruno Boutantin
Directeur Marketing Extrude Hone Group
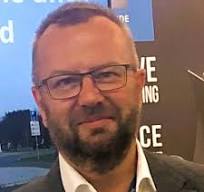